Verbundwerkstoffe vereinen die Vorteile von zwei verschiedenen Materialbereichen. Ein Material bildet die Matrix und ein anderes Material die Verstärkungsphase, wobei aus ihrer Kombination ein Verbundwerkstoff entsteht. Je nach Material der Matrix können Verbundwerkstoffe in Polymermatrix-Verbundwerkstoffe (PMC), Metallmatrix-Verbundwerkstoffe (MMC) und Keramikmatrix-Verbundwerkstoffe (CMC) eingeteilt werden. Die Verstärkungsphasen sind in der Regel härter und widerstandsfähiger als die Matrix. Außerdem können die Verstärkungsphasen kontinuierlich – wie Laminate oder Fasern – oder diskontinuierlich – wie Whisker oder Partikel – sein. Diese Seite konzentriert sich auf die Materialografie von faserverstärkten Polymermatrix-Verbundwerkstoffen.
Faserverstärkte Polymermatrix-Verbundwerkstoffe haben zahlreiche Anwendungen in der Luftfahrt- und Automobilindustrie gefunden. Ihr Hauptvorteil liegt in ihrer mechanischen Festigkeit und Zähigkeit, die richtungsabhängig verändert werden können. Durch die Kontrolle der Ausrichtung der Fasern und ihres Anteils in der Matrix können ihre mechanischen Eigenschaften gesteuert werden. Traditionell wurden Glasfasern häufig als Verstärkungsphase verwendet. In jüngster Zeit sind kohlenstofffaserverstärkte Verbundwerkstoffe aufgrund ihrer verbesserten mechanischen Eigenschaften sehr populär geworden.
Metallografie von Kupferlegierungen
Inhaltsverzeichnis
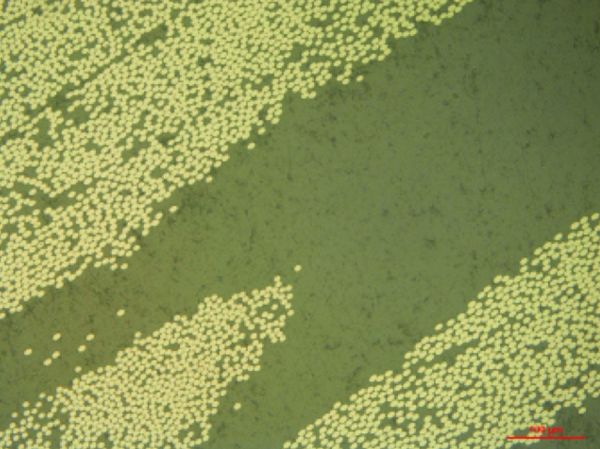
Mikrostruktur eines unidirektionalen kohlenstofffaserverstärkten Verbundwerkstoffs senkrecht zur Faserorientierung nach einem vierstufigen Polierverfahren (der Maßstabsbalken beträgt 100 µm).
1/ Materialographie
Die wichtigsten Aspekte, die bei der mikrostrukturellen Analyse von faserverstärkten Verbundwerkstoffen von Interesse sind, sind :
1. Die Verteilung der Fasern in der Matrix
2. Die Morphologie der Fasern
3. Die Defekte im Verbundwerkstoff
Defekte sind in Verbundwerkstoffen mit Polymermatrix sehr häufig und können sich sehr nachteilig auf die mechanische Festigkeit des Verbundwerkstoffs auswirken. Beim Polieren parallel zur Faserausrichtung muss besonders darauf geachtet werden, dass die Fasern während des Polierens nicht ausreißen.
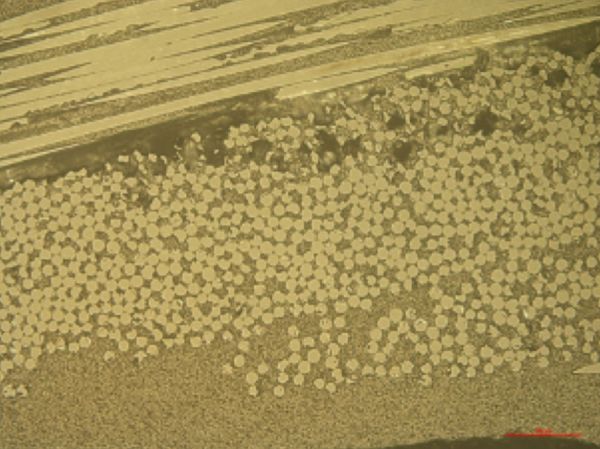
Mikrostruktur eines bidirektionalen glasfaserverstärkten Verbundwerkstoffs, die auf Defekte in den Fasern schließen lässt. und Porositäten, die von der Herstellung herrühren (Poliert nach dem in diesem Bericht angegebenen Verfahren).
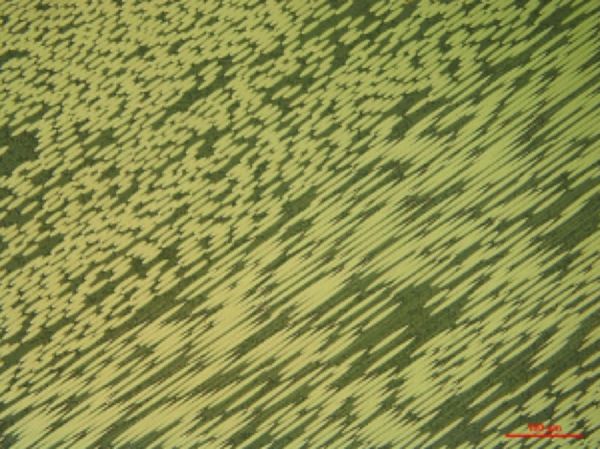
Mikrostruktur eines kohlenstofffaserverstärkten multidirektionalen Verbundwerkstoffs, die keine Defekte aufweist (poliert nach dem in diesem Bericht angegebenen Verfahren).
2/ Methoden zur Vorbereitung der Proben
Um die Mikrostruktur zu analysieren, muss die Probe präpariert werden, ohne die Mikrostruktur zu beschädigen. Im Folgenden finden Sie einige Richtlinien, die bei jedem Schritt der Probenvorbereitung beachtet werden sollten, um die Mikrostruktur richtig zu analysieren.
- Trennen
- Einbetten
- Polieren
Trennen
Faserverstärkte Verbundwerkstoffe müssen sorgfältig geschnitten werden, um eine Beschädigung der Fasern zu vermeiden, die in der Regel zerbrechlich sind. Wenn also nicht die richtigen Trennscheiben oder Maschineneinstellungen verwendet werden, kann die Mikrostruktur beschädigt werden, was zu ungenauen Interpretationen führen kann.
Trennscheiben
Zum Trennen von faserverstärkten Verbundwerkstoffen werden Diamant-Trennscheiben empfohlen. Die LAM PLAN Präzisions-Trennscheiben Schwarz bieten aufgrund ihrer Feinheit einen präzisen Schnitt und minimieren gleichzeitig die Beschädigung der Mikrostruktur des Verbundwerkstoffs. Die Schleifmittel in Diamantschleifscheiben können nach längerem Schneiden an Schärfe verlieren. Ein Abrichtstein sollte verwendet werden, um die Schneidwirkung wiederherzustellen.
Fixierung des Werkstücks
Je nach Form und Größe des Werkstücks muss ein Schraubstock oder ein Fixierungssystem gewählt werden. Die Fixierungssysteme von LAM PLAN verhindern beim Schneiden mit Cutlam-Maschinen übermäßige Vibrationen und das gefährliche Lösen der Teile von den Fixierungssystemen.
Parameter der Trennmaschine
Von den verschiedenen Parametern sind die Drehzahl der Trennscheibe und die Vorschubgeschwindigkeit am wichtigsten. Die Tabelle unten zeigt die optimale Drehzahl in Abhängigkeit vom Durchmesser der Scheibe.
Um Schäden zu minimieren, werden beim Schneiden von PMC langsame Vorschubgeschwindigkeiten, wie z. B. 0,3 mm/s, empfohlen. Einzelne Faserstränge können in der Regel mit einer Schere abgeschnitten werden.
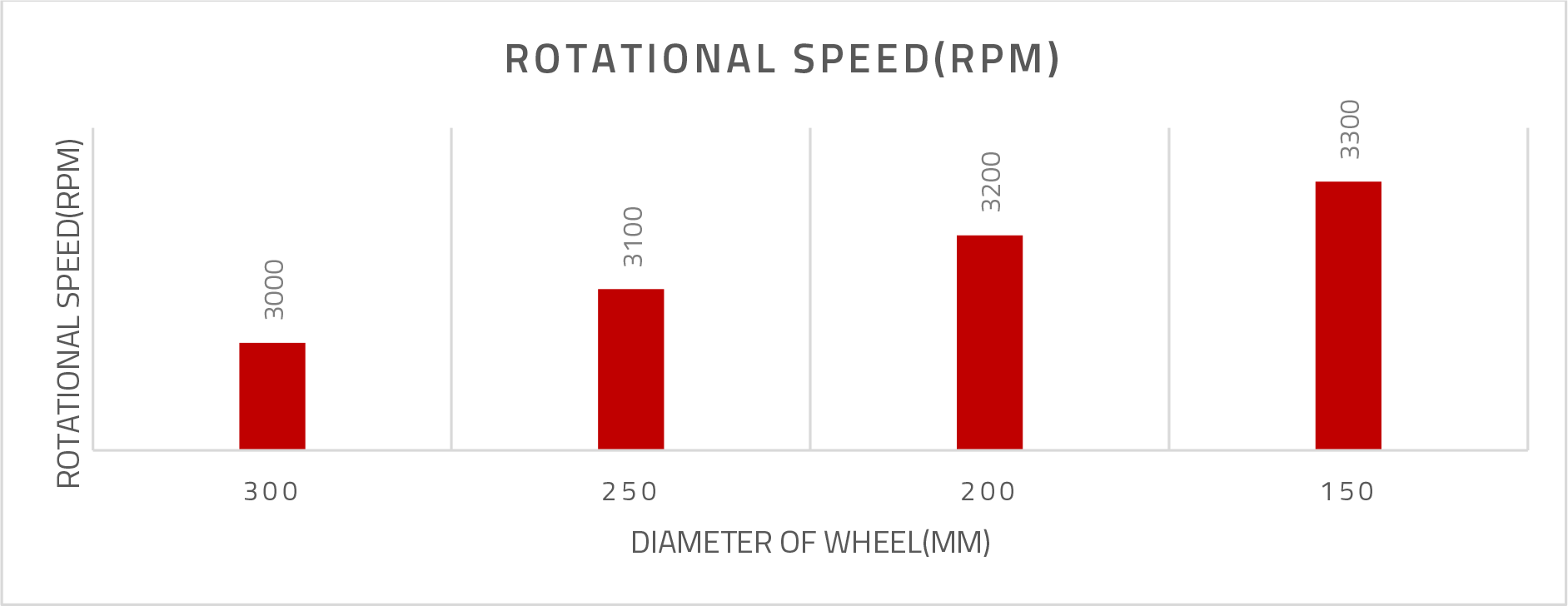
Flüssigkeit zum Trennen
Die Trennen-Flüssigkeit Lamplan 722 kann zum Trennen von PMC verwendet werden.
Einbetten
Da PMCs empfindlich auf hohe Temperaturen reagieren, werden sie mit Kalteinbettungsharz ummantelt. Ein wichtiges Kriterium für das Einbetten von losen Fasern oder Verbundwerkstoffen ist die Schrumpfung. Beim Schrumpfen des Einbettharzes kann ein Spalt zwischen Probe und Träger entstehen, der die Mikrostruktur schädigt. Der Verbundstoff muss fest in der Einbettung gehalten werden, um eine Beschädigung zu vermeiden. Zu diesem Zweck bietet das Harz 607 schnelle Einbettungslösungen. Allerdings können auch CMR-freie Epoxidharze nützliche Lösungen sein.
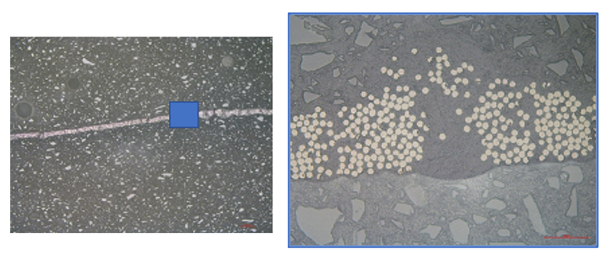
Mikrostruktur einer Schicht aus harzgebundenen Kohlenstofffasern, die zur Herstellung von Verbundteilen verwendet werden, die in Harz 607 eingebettet sind.
Weitere Informationen über alle unsere Verbrauchsmaterialien zum Einbetten finden Sie unter :
Polieren
Der erste Schritt besteht in der Regel aus einem groben Vorpolieren, um die Oberfläche der Proben flach zu machen. SiC-Schleifpapier wird häufig für das Vorpolieren von PMCs verwendet, da es einen schnellen Materialabtrag ermöglicht.
Sobald die Proben flach sind, können sie vor-/nachpoliert werden. Die Lamplan Touchlam 2TS3 Polierscheiben sind sehr effektiv, wenn sie zusammen mit den Neodia Bio Diamant-Schleifmitteln auf PMCs verwendet werden. Die Polierscheibe erhält die Planheit der Proben während des Poliervorgangs.
Beim Vorpolieren und Polieren von PMCs ist der Zentraldruck dem Einzeldruck vorzuziehen. Der zentrale Druck hält die Proben flach und verhindert das Ausreißen von Fasern, insbesondere wenn das Polieren parallel zur Faserausrichtung durchgeführt wird. Das Bild unten zeigt das Ergebnis einer Fallstudie, bei der die Ergebnisse der Verwendung von Einzeldruck und Zentraldruck beim Polieren verglichen wurden. Ziel war die Analyse von Herstellungsfehlern. Die Faserausrisse, die beim Schleifen und Polieren entstehen, verdecken andere Defekte, die nicht deutlich sichtbar sind.
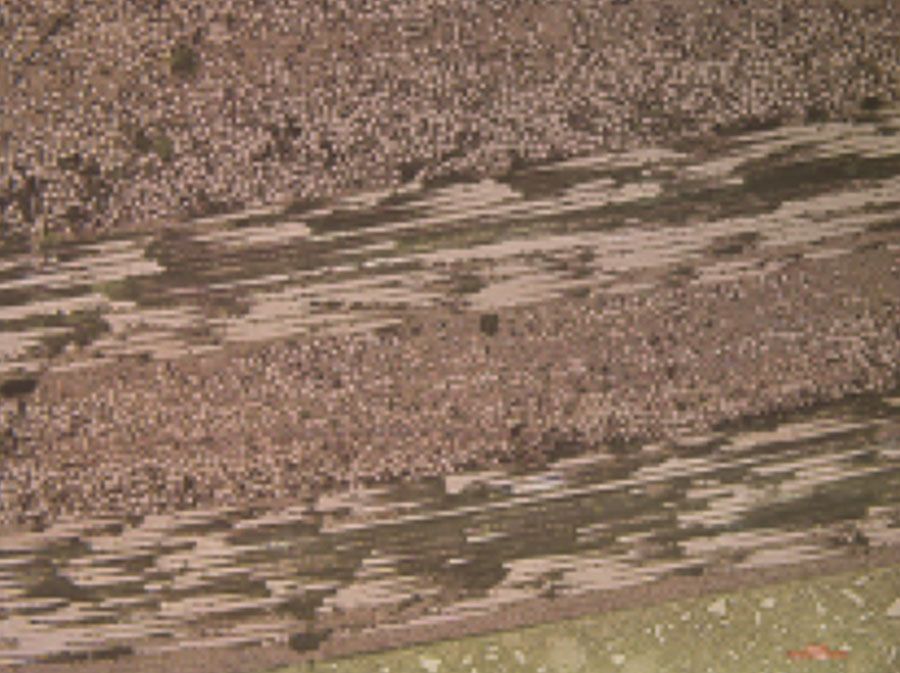
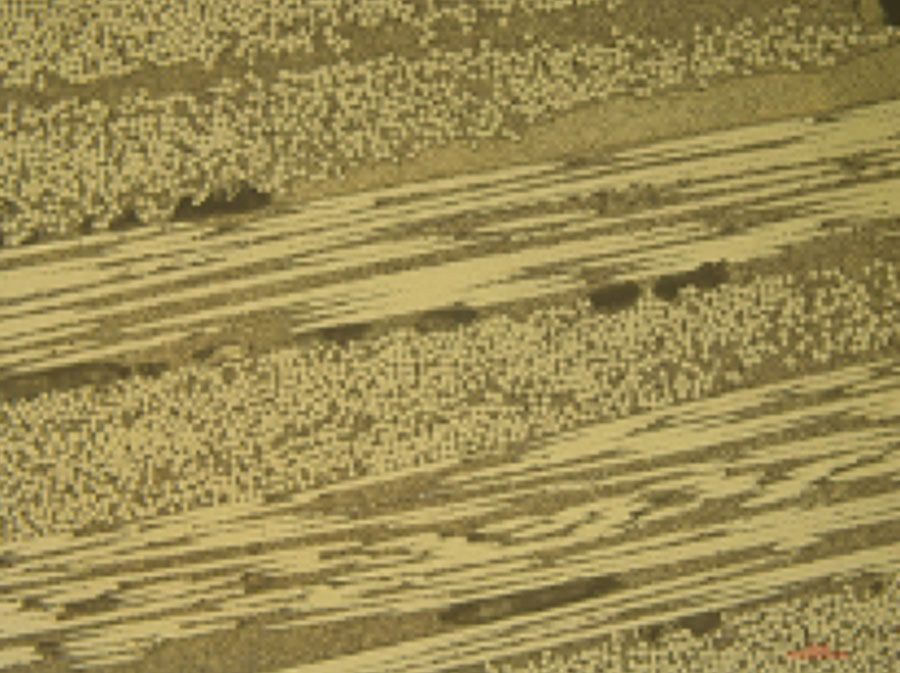
Glasfaserverstärktes PMC – einzeln druckpoliert, das beim Polieren Faserausrisse zeigt (links); zentral druckpoliert ohne Faserausrisse beim Polieren (rechts).
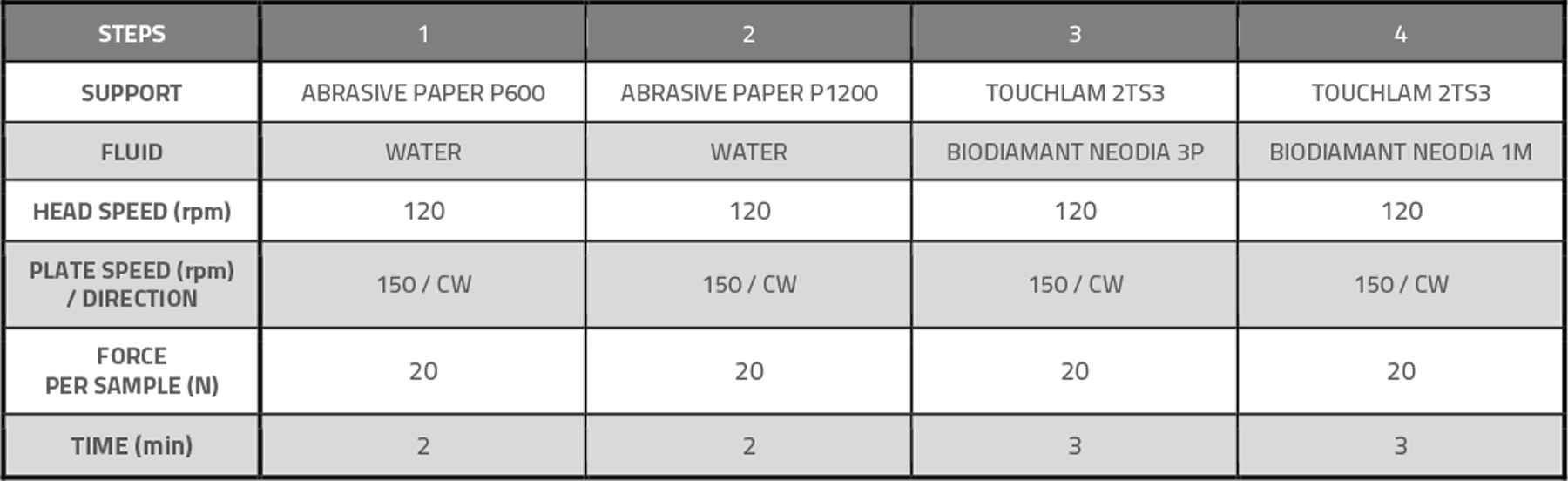
H – Uhrzeigersinn / AH – Gegenuhrzeigersinn / KOPFRICHTUNG: Immer H (die Parameter sind optimiert, um 6 Proben mit einem Durchmesser von 30 mm zu polieren)
3/ Hilfen und Lösungen
-
Kratzer bleiben nach dem Endpolieren auf der Mikrostruktur bestehen
-
Ursache(n)
• Verunreinigung der Polierscheibe.
• Schlecht gereinigte Proben vor dem endgültigen Polieren.
• Zu großer Spalt (Schrumpfung) zwischen Harz und Probe. -
Lösung(en)
• Tauschen Sie die Polierscheibe aus. Lagern Sie die Polierscheibe in einem geschlossenen Boxlam-Raum.
• Spülen Sie die Proben nach jedem Reinigungsschritt gründlich ab. Verwenden Sie vor dem endgültigen Polieren eine Ultraschallreinigung.
• Verwenden Sie Epoxidharze, um die Schrumpfung zwischen dem Harz und der Probe zu unterdrücken.
-
Verschmutzung/Spuren auf der Oberfläche
-
Ursache(n)
• Schlechte Reinigung oder Trocknung nach dem Polieren.
-
Lösung(en)
• Verwende Alkohol, um die Oberfläche der Probe zu reinigen.
• Trocknen Sie die Oberfläche gut ab.
• Verwende das LAM15-Tuch, um die Oberfläche der Probe abzuwischen.
-
Die Fasern sind nicht gut ausbalanciert
Die Fasern werden beim Polieren herausgerissen. -
Ursache(n)
• Ungleichmäßige Abnutzung von Harz und Fasern aufgrund ihrer unterschiedlichen Härtegrade.
-
Lösung(en)
• Verwenden Sie ein zentrales Drucksystem.