Metallography of some samples (with phases of varying hardness, with coatings, with intricate contours etc) demands flat polished surfaces with no form of relief or edge rounding. However, the process to grind and polish samples flat may not be straightforward. Many times, routes to having flat samples involve increasing the complexity and size of the machine. LAM PLAN having profound expertise in lapping processes, which involve rendering samples flat, proposes a simple approach to polishing metallographic samples flat. The proposed approach works for all users working on smaller samples (30 mm and lesser) needing the best edge retention and flatness.
Preparing flat metallographic samples semi-automatically at the simplicity of manual polishing
Contents
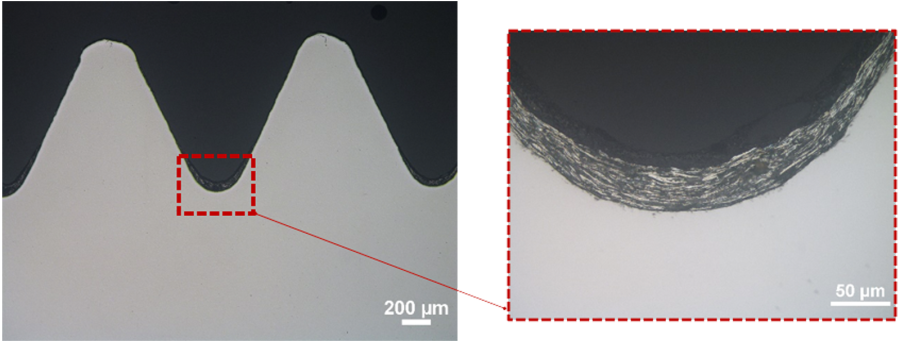
Microstructure of a steel fastener with a propriety double-layered anti-corrosion coating polished with the aid of Springlam, a novel sample-moving accessory, on a manual polishing machine. The microstructure serves as a proof that, many times, high quality results can be obtained with simple machines and tools even without compensating on the degree of automation.
Importance of preparing flat samples
Metallographic sample grinding/polishing is critical in metallographic sample preparation because of the necessity to remove any deformation in the microstructure from sectioning and to remove the scratches on the surface. This phase of sample preparation generally starts with a coarse-grinding step that removes enough material from the surface – 1. To get rid of the deformation layer from sectioning. 2. To render the samples flat for pre-/fine-polishing. Grinding operations can also induce microstructural deformation which has to be removed by the following polishing step. To minimize the damage in the microstructure to the best extent possible, both grinding and subsequent polishing are carried out with refining abrasive sizes. This means that the amount of material removed regresses as polishing progresses. This is why the grinding step has to render the samples flat so that the objective of polishing will be limited to removing the grinding scratches and deformation.
The figure below depicts the ideal grinding plane to have flat ground samples during preparation compared against a convex grinding plane that results in edge damage and non-flat surfaces with extensive scratching on the edges. A non-ideal grinding plane often results from differential material removal arising from, for example, huge difference in hardness between the resin and the sample, the kinetics of the machine, presence of multiple materials of varying hardness in the material, poor choice of consumables, etc.

Difference between polishing a sample with a flat ground surface and a convex ground surface: When the surface is convex (on the left), polishing leaves out the grinding scratches on the edges of the specimen, whereas (on the right), the grinding scratches are removed uniformly in the flat-ground specimen resulting in better edge retention.
Conventional pressure systems in semi-automatic polishing machines
Individual pressure mode
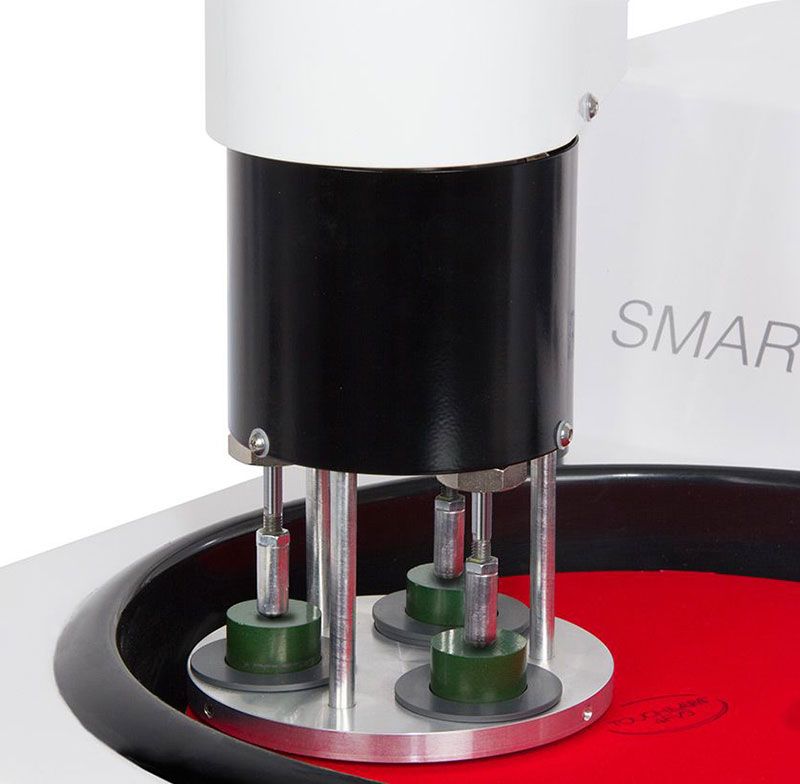
-
Pressure applied through pistons dedicated for each sample
-
Slower transition between steps owing to the placement of samples one by one at the start of every step
-
Higher possibility of samples oscillating in the sample-holder while rotating, resulting in edge rounding, differential material removal across the surface of the sample, or damage in fragile coatings
Central pressure mode
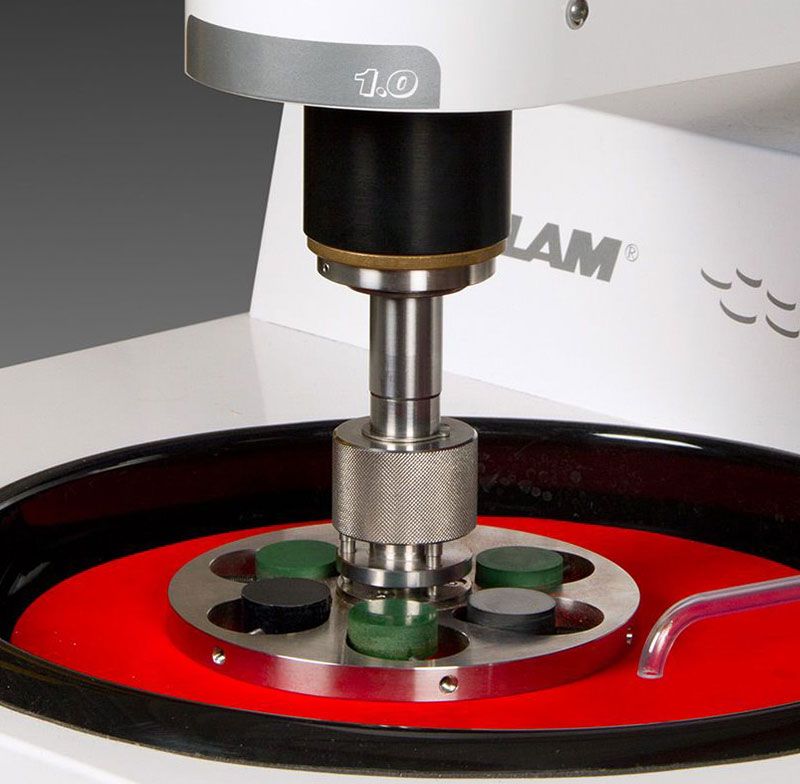
-
Pressure distributed through a central stem
-
Faster transition between polishing steps since the samples are tightened to the sample holder throughout the polishing cycle
-
Flat polishing of samples
Most metallographic laboratories, these days, are equipped with semi-automatic mechanical polishing machines that ensure repeatable and high-quality polishing results. A typical semi-automatic polishing machine has a specimen-moving head equipped with pressure systems/pistons to press the specimens against a plate containing abrasives. The pressure systems usually rely on pneumatics and are broadly categorized, depending on the pressure modes they use to exert grinding/polishing force on the samples, as Individual and Central pressure mode. The table below compares the conventional individual and central pressure modes.
Time and time again, central pressure systems have proved themselves superior to individual pressure systems for polishing soft and ductile alloy specimens or specimens with coatings. More specifically for metallography of specimens with fragile coatings and phases, specimens containing materials of widely varying hardness, and soft cold-mounted alloys, central pressure system is almost always preferred.
LAM PLAN’s unconventional central pressure polishing system
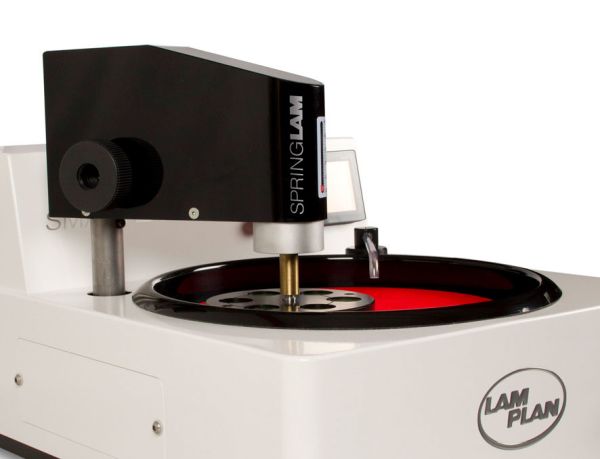
By eliminating the complexity of pneumatics and various electronic components, Springlam achieves similar results as a conventional central pressure polishing system at a reduced cost and increased simplicity.
In lapping the loaded pieces turn freely on a lapping plate with abrasives, at a speed determined by the speed of the plate. Lapping principally takes advantage of this kinetic phenomenon to produce the desired flatness with the desired surface finish. The solution is inspired from lapping in a way that, the specimen holder is allowed to rotate freely as dominated by the rotation of the plate.
Using Springlam offers three principal advantages over the conventional polishing heads:
- Improved flatness/Reduced differential material removal
In conventional polishing heads, the kinetics of the plate and the head significantly influence the flatness of the grinding plane and uniformity of material removal across the sample. When both the head and the plate turn at 150 rpm, the grinding plane is flatter than when the head turns at 30 rpm and the plate turns at 200 rpm. However, Springlam allows for the specimen holder to adapt to the speed of rotation of the plate, therefore, reducing the influence of kinetics as a whole, to have the best possible flatness. - Reduced aggressivity
The aggressivity of grinding processes in conventional polishing systems greatly depends on the difference between the circumferential speeds of the head and the plate. It is not very apparent to find the combination of head and plate speed to have the minimum aggressivity.
In conventional polishing heads, because of the kinetics of the machine, the grinding can be more aggressive than with the system such as Springlam. This is again because of reasons attributed in the previous point – the specimen holder adapts to the kinetics of the plate resulting in lesser aggressivity of the abrasion process. - Reduced complexity of machine
Since the Springlam depends solely on mechanical forces supplemented by a spring, it makes it a lot easier to install and use. The Springlam itself is an accessory adapted for SMARTLAM 2.0 which in itself is a manual polishing machine. Hence, it can be used as a plug-and-play upgrade after the purchase of the manual polisher.
The transition between polishing steps is faster than in conventional polishing heads because the sample-holder does not need to be fixed to the head. In a way it combines the pros of individual and central pressure systems.
Why not for all metallographic samples?
By not turning the samples at a fixed velocity, the improved flatness and edge retention of the samples come with a slight compensation on the material removal rate – as expected from reduced grinding aggressivity. Hence, the Springlam is an excellent choice for samples of diameters 30 mm or lesser where the polishing process does not demand extensive removal of material from the surface, as much as uniformity in material removal across the sample/coatings. Increased sample diameters necessitate removing larger amounts of material while grinding to render them flat in which case, the conventional central pressure system such as MASTERLAM suits better.
Contact us
To know more on how you can improve your polishing processes efficiently, do not hesitate to contact our technical team at: